
Pallet Wrapping Machine - Omni Cresco
Neck Down System:
The term ‘neckdown’ refers to the width reduction of the film after being stretched. The neckdown is usually higher when the film is pre-stretched but our unique rubber rollers grip and lines system has been designed to prevent the film from reducing its width while being pre-stretched therefore increase stretch yield 400%.
Power Pre Stretch Unit*:
With the ability to stretch film to 400%, this feature is unique to the Omni Pallet Wrappers.
Inbuilt Memory Technology:
This allows you to calculate your usage of stretch wrap, a perfect tool for analysing your costing per pallet wrapped and for monitoring operator usage.
Automatic Programming:
With 32 program settings, you can wrap your pallets to suit your specific needs. This ensures your pallet load is secure while maximising stretch film performance.
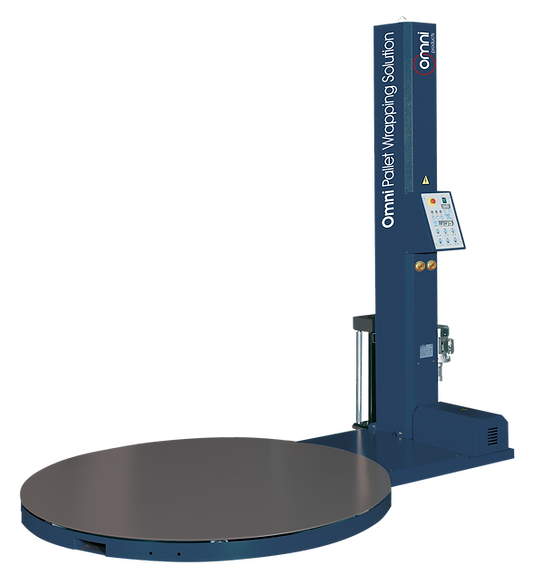
Rack & Pinion Shaft:
Unique to Omni Wrappers, this unbreakable and safe
mechanical system makes it the most reliable and high performing machines on the market.
Chain Driven Turntable:
Most pallet wrappers have a belt driven turntable. The chain driven turntable on the Omni Wrappers reduces breakdowns and makes it virtually maintenance free.
Control Panel Lock:
This gives you the ability to have a password protected control panel so there isn’t interference to the machine settings
Automatic Tension Settings:
A load cell that detects the corners of the pallet and releases the film tension to prevent crushed corners. This
ensures your pallet load is secure whilemaximising stretch
film performance. This
feature is unique to the
Omni Wrappers.
The Omni Cresco Pallet Wrapper is your perfect entry level machine which includes the core of what you will need. This machine is suitable for any warehouse situation as it has a pallet height sensor and a bottom and top turns adjustment. This affordable wrapper takes the strain away from hand wrapping.
Carriage Tilt for Low Wrapping:
This carriage tilt feature allows excellent load to bond, wrapping within 30mm from the base of the pallet.

Prevent Back injury from hand wrapping pallets

Save Wrapping costs by 20%

Reduce Stretch film usage by 50%

Increase Stretch yield to 400%

• Reinforcing operation
• 3 working cycles: ascent/descent; topsheet; only ascent
• 3 programs can be saved
• “Playback” special cycle
• 2 working ways: semimanual, semiautomatic.
• Acoustic warning at the cycle beginning and stop
• Autodiagnostic
• Powder coating
• Braked turntable at the end of the cycle
*Extra Options
- 1650 mm turntable
- 2000 kg max pallet weight
- 2500 mm wrapping height
- Ramp
- Pit frame
- Photocell for dark loads
- Power pre-stretch carriage
• Electronic printed circuit board
• Frequency controller for turntable speed adjustment (from 3 to 12 RpM)
• Frequency controller for carriage speed adjustment (speed going up and speed going down can be set differently)
• Loading plate ø 1500 mm
• Maximum wrapping height: 2400 mm
• Maximum loading weight: 2000 kg
• Electromagnetic brake for film stretching
• Photocell for pallet height detection
• Safety stop at the base of the carriage
• Stop at 0 position
• Power board IP54
• 4 digits display
• 2 access keys (including lock mode)
• Adjustable parameters by the control panel: cycle selection, bottom turns, top turns, rotation speed, carriage speed going up, carriage speed going down, film tension.
• Many parameters available at upper password level
Height 2466mm
Width 1650mm
Length 2380mm
Turntable Height 86mm
Machine Weight 400kg
Power Supply 240 Volt
Power Absorption 1kW
Weight Capacity 2500kg
Wrapping Height 2400mm
Automatic Programming: With 32 program settings, you can wrap your pallets to suit your specific needs. This ensures your pallet load is secure while maximising stretch film performance.
Inbuilt Memory Technology::This allows you to calculate your usage of stretch wrap, a perfect tool for analysing your costing per pallet wrapped and for monitoring operator usage.
Automatic Tension Settings:A load cell that detects the corners of the pallet and releases the film tension to prevent crushed corners. This ensures your pallet load is secure while maximising stretch film performance. This feature is unique to the Omni Wrappers.
Rack & Pinion Shaft:Unique to Omni Wrappers, this unbreakable and safe mechanical system makes it the most reliable and high performing machines on the market.
Power Pre Stretch Unit*:With the ability to stretch film to 400%, this feature is unique to the Omni Pallet Wrappers.
Neck Down System:The term ‘neckdown’ refers to the width reduction of the film after being stretched. The neckdown is usually higher when the film is pre-stretched but our unique rubber rollers grip and lines system has been designed to prevent the film from reducing its width while being pre-stretched therefore increase stretch yield 400%.
Control Panel Lock:This gives you the ability to have a password protected control panel so there isn’t interference to the machine settings
Chain Driven Turntable:Most pallet wrappers have a belt driven turntable. The chain driven turntable on the Omni Wrappers reduces breakdowns and makes it virtually maintenance free.
Scales in Turntable*:This eliminates double handling of weighting pallets before wrapping
Pallet Wrapping Machine Features
Receive a Pallet Wrapping Machine for free

Request a Quote & Free Trial!


Take control of your wrappers with remote app & power pre-stretch intelligence technology




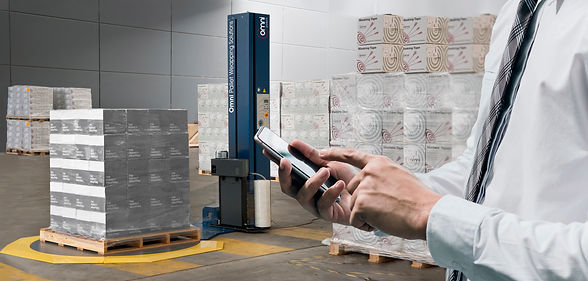
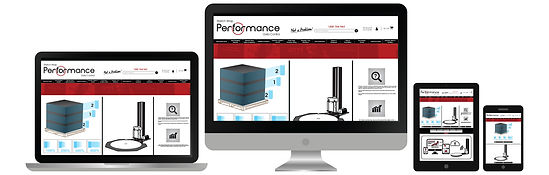




Our Omni Products have received multiple awards and certifications internationally as a result of the outstanding innovation and development of our packaging machinery and consumables.
Pallet Wrapping Machine - Award Winner

Pallet Wrapping Machines you can rely on!
Reduce costs, prevent downtime and improve reliability with Omni’s Machinery Service Solution!
-
It’s free - No fee to join our machine service membership
-
Receive an extra 3 months free warranty when you join our membership
-
All members receive a 20% discount on all machine parts and receive fixed service rates
-
Same day or 24 hour call our times for breakdowns
-
Regular pro-active machine services prevent breakdowns
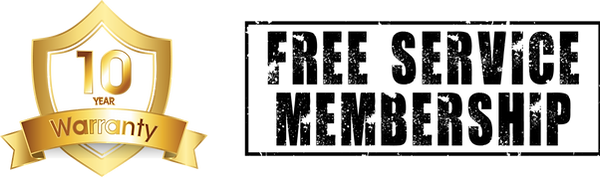