
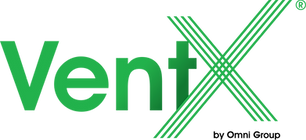
Stretch Film Slitter
Converting Regular Stretch Film Into Ventilated Stretch Wrap
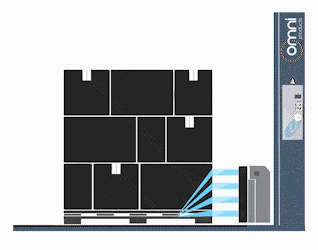
The Omni Pallet Wrappers can be fitted with a device to convert regular stretch film into ventilated wrap. This method of producing ventilated stretch film is a fraction on the cost of conventional ventilated stretch wrap. The VentX film slitter significantly reduces plastic usage and pallet wrapping cost. With a worldwide patented design, this mechanism has blades cutting the stretch wrap into 4 separate bands of film allowing the pallet load to breathe.
HALVE Plastic Usage & SAVE Wrapping Costs

Do you want to HALVE Ventilated Pallet Wrapping Costs?

Why Pallet Loads need to Breathe?
Avoid
Reduce
Prevent

Load Cooling Time
Hot-Fill Product Damage
Fresh Produce Damage
Ventilated stretch wrap is perfect for wrapping loads of fresh produce that are likely to get damaged by ripening gases, humidity and mould. Vented stretch wrap is used to prolong the shelf life of fresh produce by allowing it to breathe while in storage and transit.
Ventilated film is perfect for wrapping loads that require fast cooling. Regular stretch wrap acts as an insulation for the load, increasing cooling time. Wrapping pallets with ventilated stretch wrap allows air to flow through the pallet, cooling the load faster. With ventilated stretch wrap, freezer temperature isn’t required to be as low, therefore reducing electricity costs.
Wrapping pallets of hot fill products with ventilated stretch wrap allows the load to breath, preventing condensation and rust. Vented stretch wrap will also reduce cooling time of hot products as regular stretch wrap acts as an insulation for the load.
Reduce Chill Room Electricity Costs
Ventilated stretch wrap is perfect for wrapping loads that require fast cooling. Regular stretch wrap acts as an insulation for the load, increasing cooling time. Wrapping pallets with ventilated stretch wrap allows air to flow through the pallet, cooling the load faster. With ventilated stretch wrap, freezer temperature isn’t required to be as low, therefore reducing electricity costs.
Regular Stretch Wrap: Insulates Load
VentX Stretch Wrap: Ventilates Load
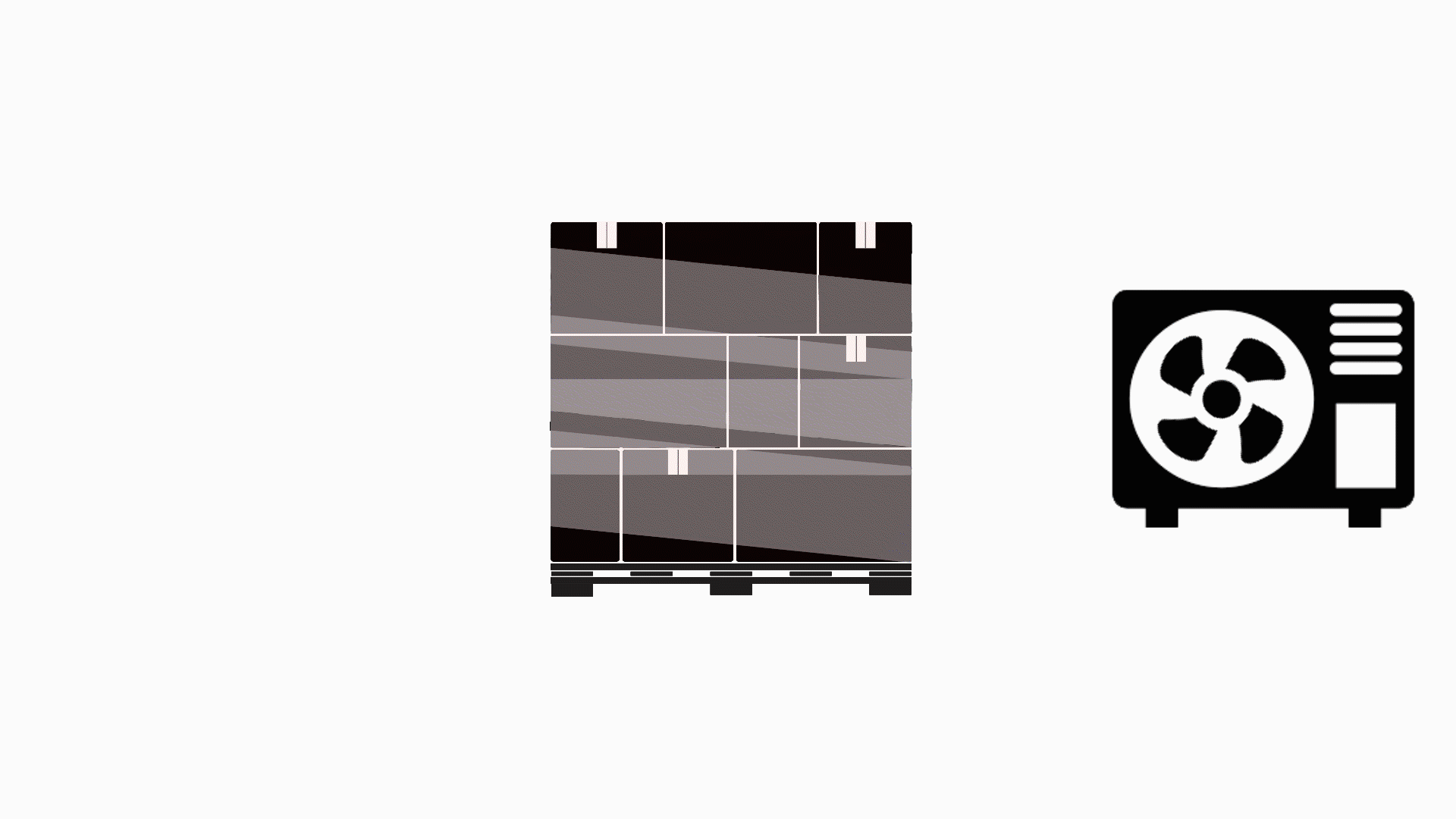
-
Load is insulated so cooling time to centre of the pallet increases
-
Freezer temperature needs to be lower to chill centre of load
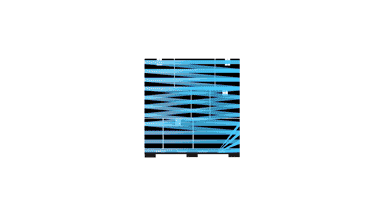
-
Reduces load cooling time as cool air can flow through the pallet
-
Freezer temperature isn’t required to be as low, reducing electricity costs
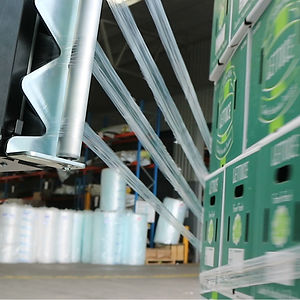
How much could you SAVE with VentX Ventilated Wrapping Solution?
5 Reasons why you need VentX Ventilated Wrapping Solution
1. Reducing stretch wrap usage reduces pallet wrapping cost
2. Improve load ventilation with larger holes to allow air to flow
3. Halving stretch wrap usage helps save our environment
4. Avoid product damage allowing product to breathe
5. Reduce electricity costs as freezer temperatures aren’t required to be as low

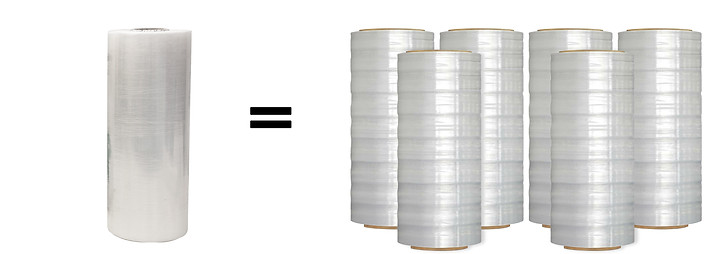
Omni Stretch Wrap with
VentX Stretch Film Slitter
1Roll - 2000m at 300% stretch
=8000m
Regular
Ventilated Stretch Wrap
6 Roll - 12000m per roll at low stretch
=8000m


*The above case study displays a typical cost and usage scenario of
egular ventilated wrap compared to the VentX Stretch Film Slitter solution
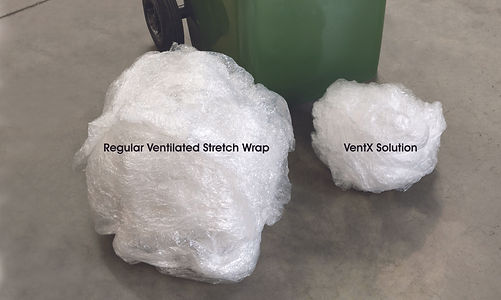
With VentX Stretch Film Slitter you will….
-
Ventilated Pallet Load
-
Halve Stretch Wrap Usage
-
Save Pallet Wrapping Costs
-
Reduce Chill Room Electricity Costs
Regular Stretch Wrap

Regular Stretch Wrap with
VentX Stretch Film Slitter

Do you want to HALVE Ventilated Pallet Wrapping Costs?
Book a Free Consultation!

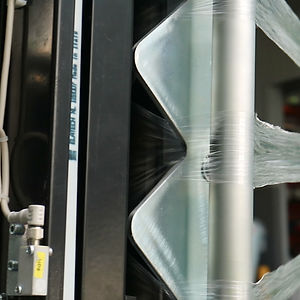