
Case Study - Franklin Web
Stretch Wrap Usage Reduced by 128 Skips Bins

Annual Cost Saving
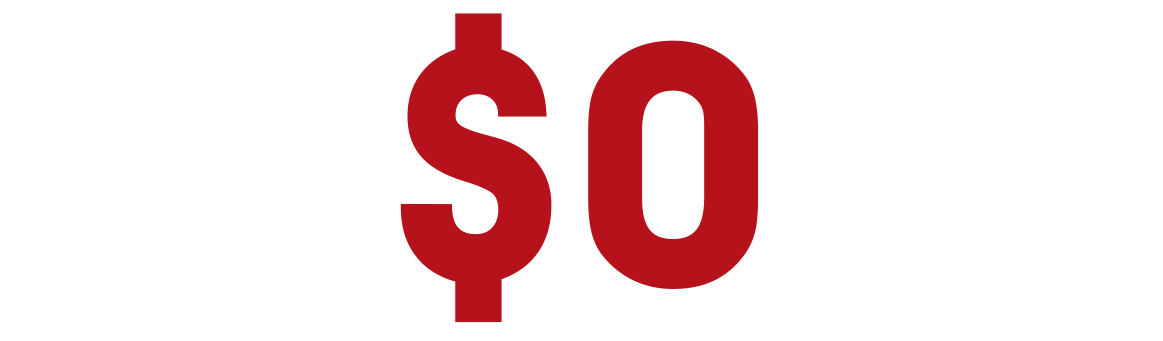
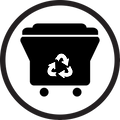
Stretch Film Reduction
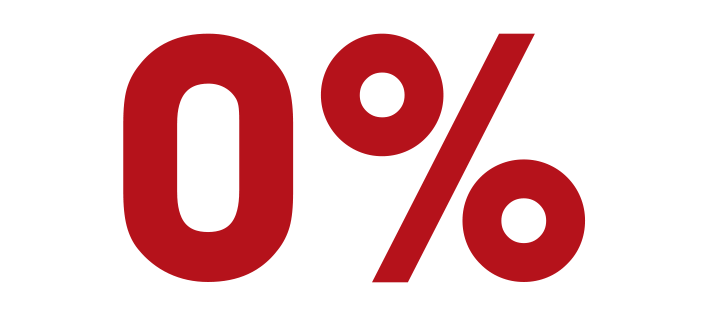
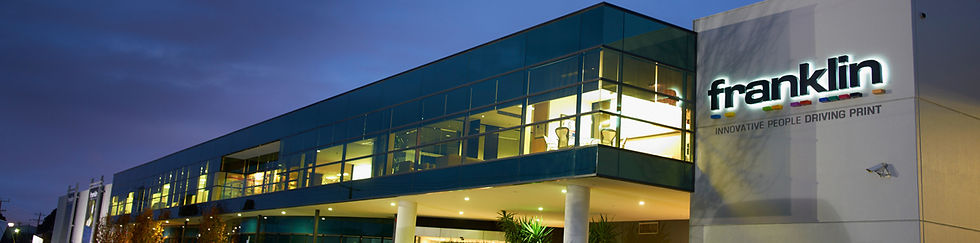
Client:

Founded in 1936, Franklin Web is one of the largest catalogue producers in the country. Operating 24 hours a day, 7 days a week at its 40-acre manufacturing plant, Franklin Web produces 250,000 pages per minute. With production volumes of this scales, it is important everything they do is the most efficient and effective method.
Franklin Web believe that attention to every detail is the key to success. Their focus is on product innovation, operational excellence and exceptional service to ensure the best outcome for our customers. To achieve that vision, it is critical for Franklin Web to partner with the most innovative and reliable suppliers.

The Problem:

The rolls of stretch wrap on their inline pallet wrapping machine has to be changed regularly causing downtime in the production line. Their stretch wrap was regularly breaking which was also causing downtime. In an attempt to eliminate this issue, they increased the thickness of the stretch wrap from 20um to 30um. Although this reduced the problem of film breakages but meant roll changes were more regular, and film usage and wrapping costs were significantly higher.
Key Problems:
-
Stretch wrap breakages causing downtime
-
Rolls of stretch wrap has to be changed regularly which was slowing down production
-
Annual stretch wrap usage was 52440kg

The Challenge:

Franklin Web operates a 40 acre manufacturing plant 24 hours a day, 7 days a week. Wrapping hundreds of pallets every day, it is important that all operations are conducted in the most efficient and effective methods possible. Cutting edge automation with minimum production downtime and labour required is critical to achieve this.
Franklin Web have a fully automatic inline pallet wrapping machine so replacing their machinery to improve power pre-stretch result wasn’t an option.
Previous Pallet Wrapping Method
Stretch Wrap Usage = 52440kg (Per Year)

The Solution:
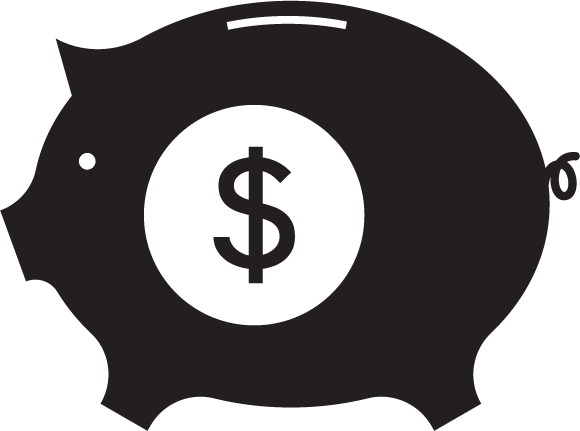
The Omni Euro Stretch Wrap was the perfect solution to Franklin Web’s pallet wrapping problems. After conducting several load containment and stretch film usage tests, Omni Group were pleased to present huge environmental and financial savings as well as significantly increasing wrapping efficiencies.
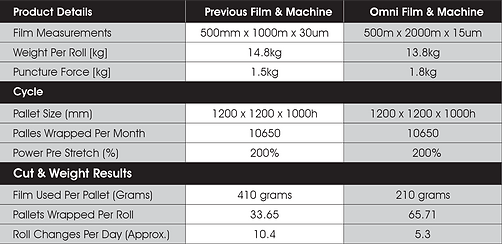
Solution Summary
Stretch Wrap Usage = 25560kg (Per Year)
-
Award winning Omni Euro Stretch Wrap
-
Roll changes reduced from 10.4 per day to 5.3
-
Stretch wrap usage per pallet reduced by almost 50%
-
Film reduction equivalent to 128 skip bins per year
-
Stretch wrap puncture force of increased by 65%
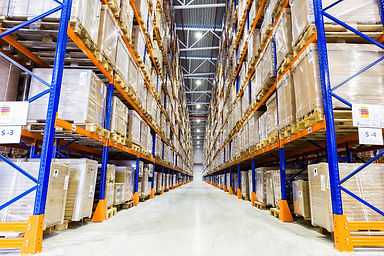
The Results:

The implementation on the Omni Pallet Wrapping Solution provides astounding financial and environment benefits for Franklin Web. A 48.8% stretch film reduction is equivalent to over 25.56 tonnes of film per year. This volume of stretch film would fill 128 skip bins every year. By increasing their stretch film efficiency Franklin Web save over $32,845 per year.
Not only did they significantly reduce pallet wrapping costs and carbon foot print, they increased their warehouse efficiency. One roll of Omni Stretch Wrap can wrap 65.71 pallets which is double the amount of the conventional stretch wrap. Less roll changes means less
pallet wrapping downtime.
“Omni Group’s philosophy is to exceed our clients’ expectations and to do more than they ask or think. Giving you what you want is our priority but exceeding what you even thought is our goal.”
Total Savings Per Year
$32,845

Cost Saving on Stretch Wrap
48.8%
Cost Saving on Stretch Wrap
25560kg =
Stretch Wrap Usage Reduction =

50%
Roll Changes Reduced by

Stretch Wrap Usage Reduction=
128 Skip Bins

